Material Control System For Reliance New Energy - SaaS
Tools: Figma
Role: UX Designer, UX Researcher

Supriya Kulkarni
Project Overview
MCS - Material Control System, the eco-conscious solution for efficient raw material management. Designed as a user-friendly SaaS web application specifically for Reliance Solar Energy Plant construction projects, MCS simplifies the process of handling raw materials.
​
With MCS, you can easily manage your daily inventory of raw materials before they head to the factory. This system meticulously tracks every transaction, from storing pallets to issuing them from storage. Plus, it streamlines material requests, ensuring you always have enough on hand without excess waste onsite.
​
In this case study, we delve into how MCS transformed the raw material management process at a reliance solar energy plant, leading to significant improvements in efficiency and sustainability. Let's explore how this innovative SaaS solution revolutionized operations and minimized environmental impact on-site.
​
(This is an MVP model presented here, which expects a more refined design after a few iterations and usability testing.)
​

Let's start with the Introduction
At Reliance, we're dedicated to creating a sustainable future through reliable, clean, and affordable energy solutions. Our new venture focuses on a diverse mix of energy sources including hydrogen, wind, solar, fuel cells, and batteries, ensuring accessibility for all.
​
Jamnagar, the birthplace of our traditional energy endeavors, now serves as the foundation for our New Energy journey. Here, we're constructing the expansive Dhirubhai Ambani Green Energy Giga Complex spread across 5,000 acres. This cutting-edge facility comprises five giga factories producing:
​
-
Photovoltaic panels
-
Fuel cell systems
-
Green Hydrogen
-
Energy storage solutions
-
Power electronics
​
The Dhirubhai Ambani Green Energy Giga Complex is poised to become one of the world's largest integrated renewable energy manufacturing hubs, marking a significant step towards our vision of a sustainable future.
In addition, we're pioneering wind power generation with a focus on scalability and cost efficiency through the development of a massive manufacturing ecosystem.
​
Our commitment to solar energy is equally robust. We're establishing a state-of-the-art, end-to-end solar photovoltaics (PV) manufacturing ecosystem in Jamnagar. This facility will be globally recognized for its technological advancement, flexibility, and cost competitiveness. From quartz to module, our 'quartz-to-module' factory integrates every step of the solar PV production process, bringing us closer to our ambitious goal of enabling 100 gigawatts (GW) of solar energy by 2030.
​
Explore more about Reliance's New Energy Mission and join us in shaping a greener tomorrow.
​
Read more about Reliance New Energy Mission
​


Process Architecture

Day Storage -
Storage space where daily required material is stored smoothen the inventory management
How did it start?
During my visit to Reliance's Warehouse and Day Storage facility, I encountered several notable challenges. The factory admin, tasked with overseeing the influx of raw materials, faced difficulties in managing the sheer volume of materials and coordinating with multiple operators. This lack of coordination led to confusion regarding where to store or retrieve specific pallets from within the facility.
​
Moreover, the absence of a comprehensive transaction tracking system hindered the admin's ability to conduct thorough cost analyses based on past material movements. Additionally, operators lacked a structured method for logging their daily operations, further complicating the overall management process.
These issues highlight the pressing need for a tailored material management system that addresses the unique operational demands of the facility.
​
​
Possible Solution
We propose developing an application designed specifically for the needs of Admins and Operators, aimed at streamlining raw material management and digitizing daily processes. Our solution involves creating a user-friendly web application where Admins can establish factory and day storage setups, while seamlessly tracking all associated data and transactions.
​
Operators will be equipped with a scanning system, enabling them to scan pallet and bin IDs effortlessly. This streamlined process will simplify both storing and issuing pallets, enhancing efficiency across operations.
Key features of our solution include:
-
Comprehensive Dashboard: Accessible to Super Admins and Admins, the dashboard offers detailed analysis capabilities, empowering informed decision-making.
-
Operator-Focused Transactions: Operators will only be authorized to conduct transactions within their designated day storage areas, ensuring accountability and accuracy.
​
By implementing this solution, we aim to revolutionize material management, promoting efficiency and transparency throughout the process.
​
​
Design Process
User Research
Personas
Understanding the users
User Research
I conducted user research to learn about the issues and requirements that admins and operators currently face when managing transactions manually. Online surveys, in-person interviews, quantitative research and usability testing were all used in the research.
During my research, I discovered that the majority of users struggle to find out past transactions and do the cost analysis accurately. Additionally, they expressed dissatisfaction with the absence of digitalisation of this process.
Additionally, the research revealed that many users were happy to use digital products like computers and scanners so that manual efforts and time would be saved.
According to the quantitative research, there is a clear need for a web app that makes it easier for users to do transactions using scanners and analysis of data digitally.
-
Quantitative Research
During the quantitative research phase, users ranging from 20 to 50 years old were asked a series of questions.
The resulting data provides insights into the level of agreement among participants regarding the posed questions.
Research Insights
1
Efficiency Metrics
​
Quantify the time spent by factory admins and operators on managing raw materials before and after the implementation of the material management system to measure improvements in efficiency.
2
Error Reduction
​
Assess the frequency and severity of errors in material storage and retrieval tasks to determine the impact of the system on error reduction.
3
Cost Analysis Improvement
​
Analyze the admin's ability to conduct thorough cost analyses based on the data provided by the material management system to assess improvements in cost management processes.
4
Daily Operations Logging
​
Determine the extent to which the structured method provided by the system improves the accuracy and completeness of daily operations logging by operators.
Persona


-
KPIs (Key Performance Indicator)
After conducting thorough research and persona analysis, I have identified four key performance indicators (KPIs) that must be met by the end of this product development phase. These KPIs are strategically chosen to align with both the business objectives and the needs of the users, ensuring a successful outcome for all stakeholders involved.
1. Inventory Accuracy Rate: The percentage of inventory records that accurately reflect the physical inventory.
-
Rationale: Addressing the pain point of manual record-keeping for admins and the risk of errors and discrepancies for operators, improving inventory accuracy ensures reliable data for decision-making, minimizes stockouts, and reduces operational disruptions.
-
Measurement: Conduct regular physical inventory counts and compare them with system records to calculate the accuracy rate.
2. Inventory Turnover Time: The average time taken for inventory items, including pallets, to move through the warehouse from receipt to issue.
-
Rationale: Targets the pain point of time-consuming processes for both admins and operators, reducing inventory turnover time improves operational efficiency, enhances production agility, and minimizes storage costs.
-
Measurement: Track the time taken for each inventory item from receipt (arrival) to issue (departure) using timestamps or RFID tracking.
3. Real-time Inventory Visibility: The extent to which inventory levels and locations are visible and accessible in real-time to admins and operators.
-
Rationale: Addresses the lack of real-time visibility highlighted for admins and operators, enhancing real-time inventory visibility improves decision-making, enables proactive inventory management, and reduces the risk of stockouts or overstock situations.
-
Measurement: Assess the frequency and accuracy of inventory updates in the system, ensuring that admins and operators have up-to-date information on inventory levels and locations.
4. System Adoption Rate: The percentage of users (admins and operators) actively using the MCS as part of their daily operations.
-
Rationale: Reflects the success of implementing the WMS in addressing the needs and pain points of admins and operators, high system adoption indicates user acceptance, engagement, and perceived value of the system.
-
Measurement: Monitor user logins, interactions, and feedback to gauge the level of adoption and identify any barriers to usage that need to be addressed.
By focusing on these KPIs during the development of the material control system, organizations can effectively address the pain points identified for admins and operators, leading to improved operational efficiency, inventory accuracy, and overall warehouse performance.
User Flow
Information Architecture
Starting the Design
Wireframes
Design System
User Flow

Information Arcitecture


Wireframes
-
Admin Flow





-
Operator Flow





Design System



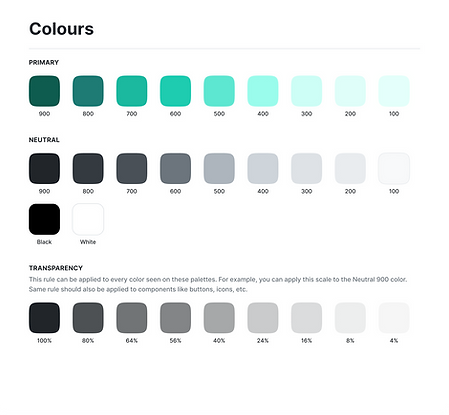
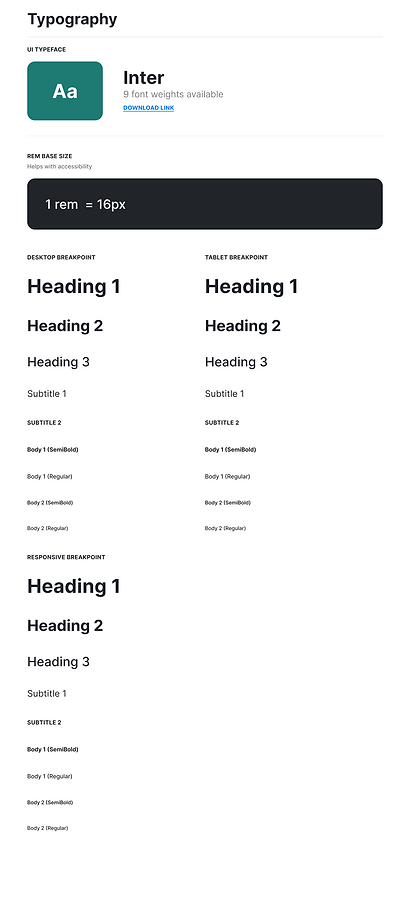


Designs (MVP)
-
Admin Flow



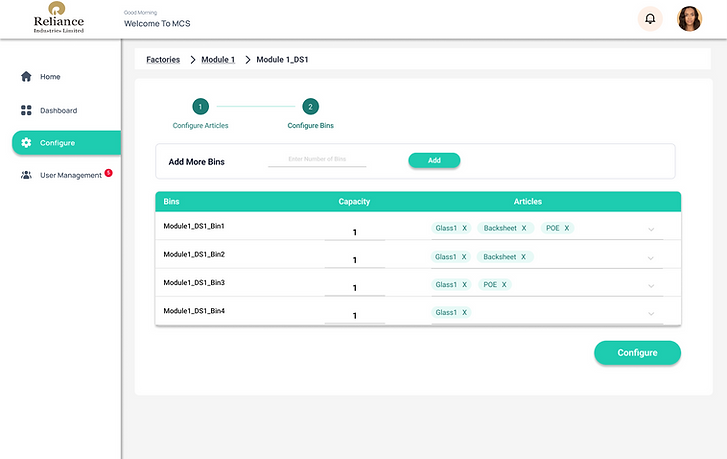




Key Takeaways
In conclusion, our team has achieved a significant milestone by delivering the initial version of an all-encompassing dashboard application tailored for warehouse management. This application caters to two distinct user groups: admins and operators. Throughout the development process, we conducted rigorous usability testing within the organization, as the application serves as an internal tool. This collaborative effort has resulted in the creation of a user-friendly and efficient solution that addresses the specific needs of warehouse management, paving the way for improved operational efficiency and enhanced user experience within the organization.
Thank You for reading so far
Any suggestions will be always welcomed here